Keeping Track of your Warehouse Management
Tips & Tricks • 3 min read • May 4, 2022 4:02:00 PM • Written by: Amelia Inskipp
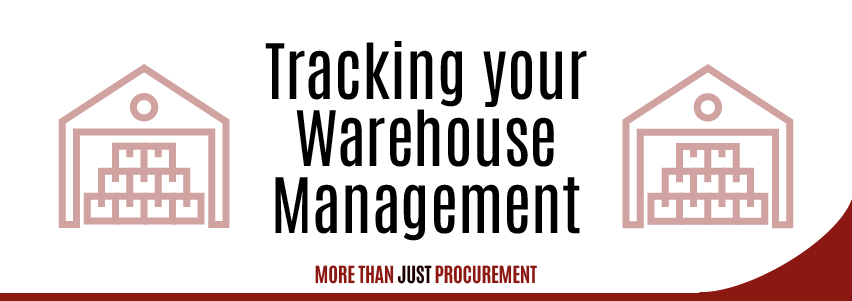
Warehouse Managers have a vast number of processes to go through. These start before an order is placed and carry on long after the order is fulfilled. Keeping on top of all these procedures and making sure each is running effortlessly is often not viable on top of their busy schedule.
Tracking your Warehouse Management
Whilst there is no one size fits all for how a warehouse should be run, below are some solutions to help keep your warehouse running as smoothly and efficiently as possible.
Stock Availability
Supply issues are sometimes inevitable for warehouses. Our about preparing for crisis provided tips on how unpreventable situations can be planned for. However, for more situations, specifically about stock, many measures such as forecasting and prioritising stock can help supply availability.
Suppliers and clients are at the forefront of business as they are what keeps a business running. Nurturing these relationships with suppliers/clients can help them help you. Being transparent about future and current orders can help provide a clear picture of the current situations. Having regular, open discussions about these types of situations can not only help build these relationships but also paint a picture of what you need and when to help forecast future orders.
Not only is it supplier/client relationships that are crucial but also sales and production departments. Ensuring they are communicating on a regular basis, can allow for both teams to forecast stock availability. Trends are also a key indicator when forecasting. Trends could be anything from seasonal demand, such as rainy seasons and the demand for drainage systems, or stock items with trend demands such as PPE in demand during coronavirus.
Heightening Accuracy
Tracking inventory is becoming critical to warehouse management with increasing expectations from clients. Without inventory checks, it can lead to failing to fulfil deliveries for clients, therefore losing money and potentially losing clients. With warehouse automation, it can eradicate the possibility of human error, increasing inventory management accuracy whilst also saving employees time to work on high priority tasks.
Not only do warehouse management systems (WMS) allow for more accuracy in inventory, but also improve picking optimisation. WMS generate picking lists displaying real-time information on the availability of stock allowing more accuracy when processing orders.
When executing warehouse procedures, performing multiple tasks at once increases the likelihood of repeatable actions, therefore increasing labour costs and not using time efficiently. Using technology to improve these operations can therefore allow control over all aspects of warehousing.
Tracking KPI’s
Key performance indicators (KPIs) are vital when keeping on track. Warehouse management systems KPIs allow specific processes to be analysed and measured against previous operating benchmarks. There are many different KPIs that can be applied to most warehouses, however, not every KPI is used to reach your specific business goals. Some include warehouse inventory, inventory to sales ratio, order management, putaway accuracy and even safety.
The inventory to sales KPI provides the ratio of remaining stock at the end of the month to the sales at the end of the same month. This is beneficial to warehouse management as it can predict potential cash flow issues if inventory is rising but sales are dropping. It can also help forecast inventory and you are then able to calculate how much stock you need to comfortably continue sales.
Putaway is the process of storing delivered products in the most convenient location in your warehouse. These KPI’s such as accuracy, cost per line, and cycle time measure how well these processes are performing. Putaway cycle time is the average time it takes to put away a single item of your inventory, the shorter the cycle time the better warehouse efficiency. Tracking these KPIs can benefit employee productivity by repositioning items in your warehouse if the cycle time is too long.
Order management consists of every single process that takes place from when the customer places an order to even post-sales processes. These KPIs are centred on how smoothly each procedure is running. Some of these KPIs can include picking accuracy, lead times, fulfilment accuracy and rate of returns. Applying warehouse management KPIs gives a clear indicator of how smoothly operations are running in your warehouse over a period of time. Not only can this help optimise the way the warehouse is run but can also allow for the discovery for areas of improvement within the warehouse allowing for better efficiency.
Managing a warehouse is not easy and does take a substantial amount of work for systems to run smoothly. Not all of these tips may help your warehouse due to every warehouse being run differently. However, utilising just a few of these tips can help keep processes under control.
Reach the World. Giving Made Easy with Impact.
Amelia Inskipp
Related Articles
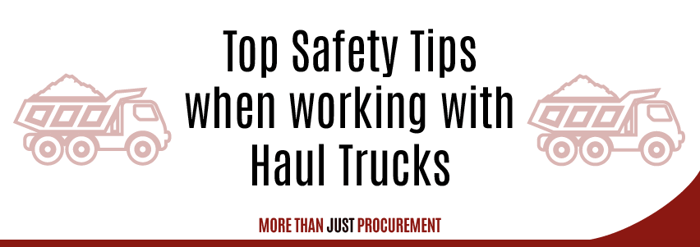
Tips & Tricks
Top Safety Tips when working with Haul Trucks
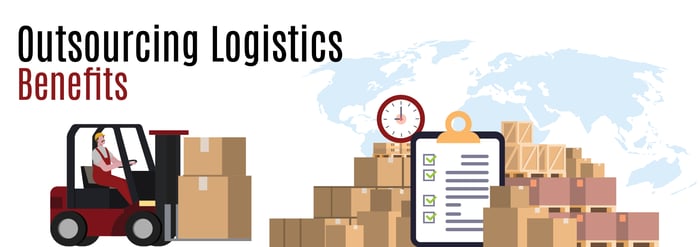
Tips & Tricks
Outsourcing Logistics Benefits
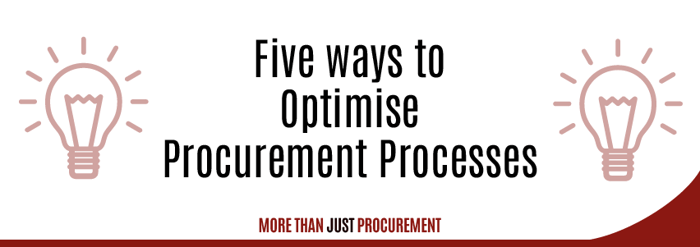
Tips & Tricks
5 Ways to optimise procurement processes
Don't Miss Out On A Thing
Sign up and Join Our Newsletter Today